Pilot study describing the design process of an oil sump for a competition vehicle by combining additive manufacturing and carbon fibre layers
Keywords:
Oil sump.
additive manufacturing.
Fused deposition modelling.
ABS plastic.
Carbon fibre.
Computational fluid dynamics.
Publisher:
TAYLOR & FRANCIS LTD.
ISSN:
1745-2759
10.1080/17452759.2015.1076240
Citation:
Cazón, A., Prada, J. G., García, E., Larraona, G. S., & Ausejo, S. (2015). Pilot study describing the design process of an oil sump for a competition vehicle by combining additive manufacturing and carbon fibre layers. Virtual and Physical Prototyping, 10(3), 149-162.
Statistics and impact
0 citas en

0 citas en
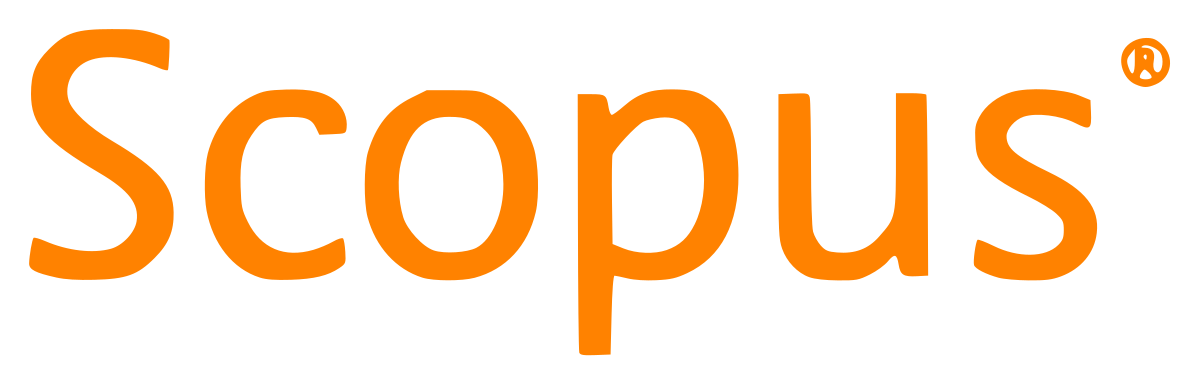
Items in Dadun are protected by copyright, with all rights reserved, unless otherwise indicated.